Те са 6 км и ги свързват още 100 км пътища под земята в рудник "Челопеч"
Като стане дума за миньор, най-вероятно първата асоциация е за човек в изпоцапани дрехи и покрито със сажди лице, хванал ръчен къртач. С него пробива тесен тунел, за да стигне до рудата. А когато се добави, че мината е за злато, в образа изплуват и кюлчета от благородния метал.
В “Челопеч” обаче се работи по съвсем различен начин. Благодарение на съвременни технологии процесът е автоматизиран и с висока продуктивност. Работниците са в чисти дрехи и им се налага по-скоро да разбират от компютри, а не толкова от къртачи. Това видя екип на “24 часа”, който прекара близо 5 часа под земята в рудника на “Дънди Прешъс Металс” в Челопеч.
За добива на злато там всъщност са необходими руда, въздух, вода и безжичен интернет. Това се случва под два хълма в Стара планина до с. Челопеч, като дълбочината на изработките стига близо 1000 м.
Рудникът в Челопеч попада сред средно богатите в света, като показателите на тон руда са 3-3,5 грама злато, среброто е 7-8 грама, съдържанието на мед е 0,95-1%. От най-богатите рудници в света добивът е 8, 9, 10 грама злато на тон руда. В Челопеч на година
се добиват 2 млн.т
руда, от която
се извличат мед,
злато и сребро
От откриването си през 1954 г. рудникът е преработил близо 19,8 милиона тона руда.
През 1971 г. държавното предприятие достига 100 хил. тона годишен добив. След приключването на програма за разширение и изграждане на нова обогатителна фабрика през 1976 г. производството се увеличава четири пъти. През 1988 г. годишният добив е в размер на 512 000 тона, след което настъпва рязък спад в периода 1990 - 1992 г.
Произведеният концентрат започва да се продава на международните пазари за последваща преработка. През 1999 г. рудник “Челопеч” е приватизиран и 75% от акциите са купени от холандската “Наван Бългериън Майнинг”.
В периода 1999-2002 г. поради несигурни пазари, ниски цени и амортизирано оборудване групата “Наван” търпи загуби и изпада в несъстоятелност. В края на 2002 г. е поставена под административен надзор. Независимо от това, добивно-преработвателните дейности продължават през 2002 и 2003 г.
През 2003 г., “Дънди Прешъс Металс” чрез своите дъщерни дружества придобива активите на “Наван Майнинг”, които включват предприятието в Челопеч. Тогава името му е “Челопеч Майнинг”, но през 2013 г. е променено на “Дънди Прешъс Металс Челопеч” ЕАД.
За периода 2004 – 2010 г. преработката на руда нараства двойно - от 521 хил. тона руда до над 1 млн. тона. Така с инвестиции в производството от над 850 млн. лв. от един банкрутирал рудник “Челопеч” се нарежда сред най-добрите в света.
Средства и усилия са вложени и в подобряването на инфраструктурата. Влизането в рудника през шахти с асансьори е минало. Преди 2004-2005 г. тежките машини са нарязвани на части, преди да влязат в рудника. Следвало е събиране на частите и запояването им.
“Всяка машина струва по 1-1,5 млн. долара. Представете си как нарязваш няколко чисто нови “Бентли” и след това ги сглобяваш наново” – казва Цветомир Велков, оперативен директор на “Дънди Прешъс Металс Челопеч”.
Сега, за да стигнеш до дълбините на рудника, можеш
да пътуваш с
минен автобус
и да избереш една от двете “магистрали” – наклонена галерия “Надежда”, дълга 2 км, и “Вяра”, с дължина 4 км.
За да бъдат прокарани тези пътища, са използвани почти всички възможни методи – изкопаване с багери, с комбайни, пробивно-взривни работи, инсталирани са много и различни крепежни конструкции.
“Такъв тип изработка е стандартна за Австралия, но е първият в България. Минали сме през глина, през стари минни изработки, през неконсолидиран масив, през силно разрушени и през здрави скали” – казва Велков.
“Стените са покрити с бетонова смес и пластмасови фибри, които придават допълнителна здравина. Като се запечата, скалата спира да диша, това не ѝ позволява да се разрушава” – казва Стилиян Минкин, главен инженер на рудник “Челопеч”.
Скалите са свързани с метални анкери, така че блоковете да не могат да се разместват.
“Това е все едно шиеш. Най-просто казано. Отделни скални блокове, разделени от пукнатини, ти ги зашиваш един за друг. Това е активен начин на закрепване на минните изработки”, обяснява Велков.
“Тялото, ако няма скелет, ще се разпадне. Това е същото”, допълва го Минкин.
Преди обаче да се качиш на буса или на някой от пикапите “Тойота”, които се движат под земята, задължително преминаваш през инструктаж по безопасност и биваш екипиран със специален гащеризон с предпазно покритие и светлоотразителни ленти. Оборудват те с каска и минна лампа с чип, така че да има проследимост в тези 100 км галерии.
В екипировката е включен и самоспасител (апарат, който осигурява кислород за 30 минути).
Движейки се в рудника, преминаваш през врати, които се отварят автоматично чрез сензор. Цветомир Велков разказва, че това са вентилационни врати, които осигуряват правилното движение на въздушната струя. Допълва, че ако не се задейства сензорът, вратите могат да се дръпнат с въжета, да се отворят с хидравлична помпа или пък да се обадиш в оперативния център на повърхността, откъдето да ги отворят дистанционно.
Ако по някаква причина и тези действия не сработят, се използва евакуационната вратичка.
До 2004-2005 г. рудата се изземва чрез прилагането на система с подетажно обрушаване. При тази технология на добив зоната, от която се иззема скална маса, не се запълва. Тогава по логиката, че природата не търпи празни пространства, масивът наоколо започва да пропада. Така с времето този участък се разширява и стига до повърхността, теренът се нарушава, а масивът се разхлабва.
“Обрушаването обаче води до влияние и върху природата, рудата се замърсява и обеднява. Работи се в среда, в която не се взима чиста руда, а смесена със стерилни скали - такива разположени встрани, извън основното рудно тяло”, разказва Цветомир Велков.
“Тази система е много по-евтина и има по-малко изисквания от гледна точка на дизайн. Но е много по-неефективна от гледна точка на начин на изземване на полезното изкопаемо. Това трябва да се случва по най-безопасен, правилен начин и с най-малко влияние върху околната среда”, обяснява Велков.
Така се взима и решението да се смени системата на разработка - от подетажно обрушаване към камерна система със запълване. Новата технология изисква много повече инженерни познания и по-сложно управление на процеса. На първо място обаче е много по-безопасна и щадяща околната среда, а и извличането на рудата е по-ефективно. Интересното е, че когато е направена тази сериозна крачка, работният процес не спира. Хората обаче трябва да знаят всички изисквания за безопасността при новия начин на работа.
“Ти пращаш един човек долу и му казваш, днес ще работиш така, а утре - по друг начин”, разказва Велков.
Компанията инвестира милиони в обучението на своите почти 1000 служители, а така се гарантира работа без инциденти.
“През 2005 г. казвахме, че животът на рудника е 10 години. Днес обаче– казва инженерът, - ако ме попитате колко е - животът му е до 2025 г. Причината е, че проучвателните ни дейности разкриват нова руда. На година се правят по 40 км ядково сондиране, за да се опознае по-добре находището”
На месец се
прокарват по 500 м
галерии или
6 км на година
Така наречените добивни галерии са дълбоко под земята. Първо се разчертава шахматно каре, след това се пробиват взривни дупки, които се зареждат с взрив, след което се взривяват.
Машината, с която се пробиват взривните дупки, се нарича карета. В т. нар. паспорт предварително се разчертава схема, по която се работи. Новите машини работят с лазер, защото най-важно е да се спазва посоката, по която ще се пробива.
“Интересно е, че машините от най-ново поколение имат вградени сензори така, че ако човек се приближи до машината, тя го засича и автоматично спира да работи. Следва зареждането с взривното вещество. Взривяването е милисекундно, което позволява общото количество взрив да бъде разделено на малки порции. Скалата се раздробява на дребни парчета, след което се извозва”, разказва Велков.
Преди обаче да се взриви каквото и да е, се проверява чрез чиповете в минните лампи дали няма останали хора след смяната. Това се следи в оперативния център на повърхността, където на монитори се вижда местоположението на работниците и оборудването.
Ако всичко е наред, след края на първа смяна, около 14 ч, се извършва взривяването. Самото взривяване се извършва през Wi-Fi дистанционно от повърхността.
За да е чисто и проветрено за втората смяна, се включват огромни вентилатори, които се управляват от повърхността. Всичко, включително и вентилацията, се наблюдава от оперативния център в реално време. В случай на инцидент от този център може да се подаде сигнал за тревога. В случай че високите технологии не сработят, има и алтернатива – чрез вентилационната система по галериите се пуска газ с аромат на вкиснат лук, който известява за аварийна ситуация.
След взрива започва извозване на раздробената скала и се прави укрепване с анкери. Извозването на рудата от камерите става с челен товарач - тежка машина, която в кофата си събира 10 тона руда. Операторът я закарва до мястото за работа в камерата и я управлява дистанционно. Чрез таблет в кабината операторът получава и отчита задачите за деня. “Машината се управлява като детска играчка. Разликата е, че тежи 43 тона” – шегува се инженерът.
Без значение дали операторът е вътре, или управлява отвън, ако вратата не е плътно затворена, машината не тръгва. Ако останат по-големи парчета скали, те се раздробяват допълнително. След това през бункер рудата стига до подземната трошачка, там се надробява на по-малки късове, след което се подава към гумено-транспортна лента. Огромен магнит над гумената лента почиства металните отпадъци от рудата. След натрошаването, по 4 км транспортна лента рудата поема към повърхността. Следва смилане в обогатителната фабрика и процес на флотация. Той може да бъде обяснен най-лесно, като се сравни с автоматично изпиране. Машините действат на принципа на пералнята - има реагенти, вкарват се въздух и вода. Образуват се металносиви мехурчета, по които полепват минералите, съдържащи злато, сребро и мед. Тези мехурчета излизат най-отгоре и преливат. Следва процес на сгъстяване и филтроване и се произвежда концентрат, който може да е меден и пиритен. Ценните метали в концентрата са мед, сребро и злато. Извличат се около 55% от златото. В България от 1 април 1990 г. е забранено да се преработва концентрат със съдържание на арсен. Затова концентратът се товари на специални вагони, които стигат до Бургас, а оттам с кораби концентратът заминава към Намибия и Китай. Част от отпадъка след флотацията се връща в рудника, за да се запълни с нея иззетото пространство, друга част отива по тръба към хвостохранилището. То е на площ от 750 дка.
“Дънди Прешъс Металс”
имат и патент при
използването на Wi-Fi
връзка под земята
Това води и много експерти от различни рудници по света в Челопеч, където черпят опит от представителите на българското предприятие.
100% от подземните изработки са с интернет връзка. Бели пластмасови кутии подават сигнал към таблетите, пробивните машини и челните товарачи. Така в реално време се следи какво се случва и вместо да се отбелязва на хартия, прогресът се вижда на екран. Там, където задачите се изпълняват според плана, на екраните в оперативния център свети зелено. Където цветът е оранжев, значи, че има изоставане и трябва помощ. Види ли червен цвят, началник - смяната отива, за да провери какво се случва.
Графиците и плановете се изпълняват в рамките на месеца или в средносрочен план – до три месеца. Обратната връзка се получава веднага, затова наваксването може да стане дори от следващата смяна. Под и над земята в предприятието има камери- общо 300. През годините “Дънди” изграждат 100 км подземна инфраструктура. В рамките на една смяна началникът преминава около 60-70 километра, за да проследи всички процеси, които се случват.
Ако някой от операторите на машините или работниците не е в добро настроение, може да ползва стресконтрола. Това всъщност е голяма
боксова круша
със снимки на всички
началници и
инженери
Веднъж се наложило снимките на боксовата круша да бъдат подменени. Един от работниците се пошегувал дали може да освободи стреса си директно върху него, разказва самият инженер Велков.
Такива разговори са ежедневие между 1000-та работещи в рудника. Въпреки че екипът е многоброен, инженерите поздравяват всички, познават ги и поименно. Атмосферата е приятелска, колегите разменят шеги.
Без значение на какво ниво в йерархията е, всеки минава през дрегер на входа на рудника. Ако са отчетени над 0 промила, дори да е шефът на предприятието, инспектор или гост, той няма да прекрачи прага. Това е едно от първите правила за безопасност, въведени от “Дънди Прешъс Металс”. Инцидентите са рядкост, а за такива, между другото, се смятат и дори човек да си одраска ръката. Събитието веднага се регистрира и съобщава. За 2016 година рекордът в предприятието е 215 дни без трудови злополуки.
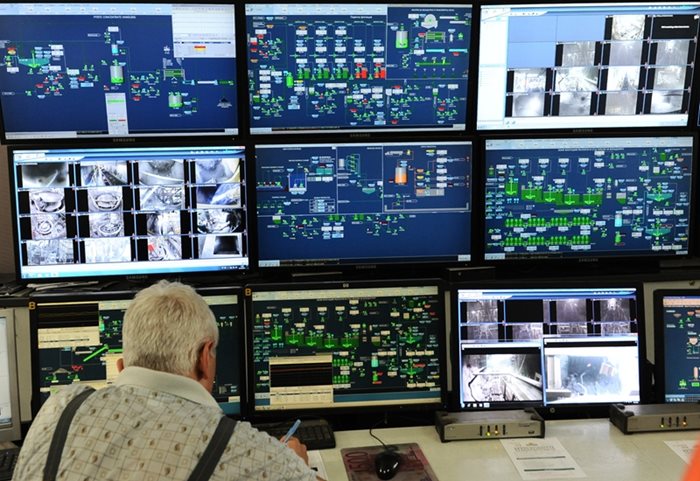

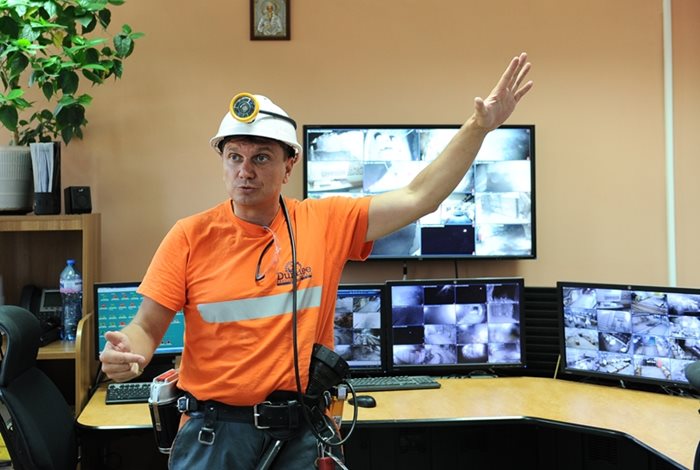
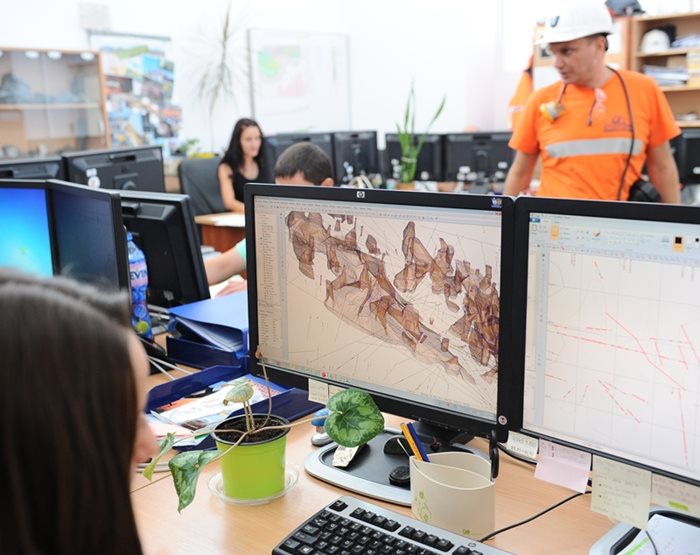

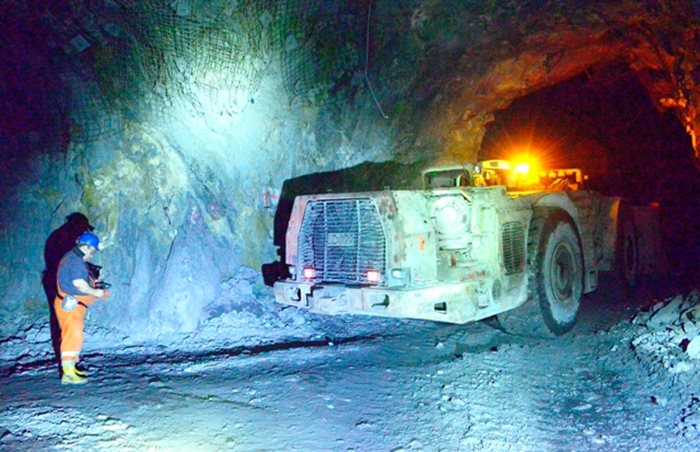
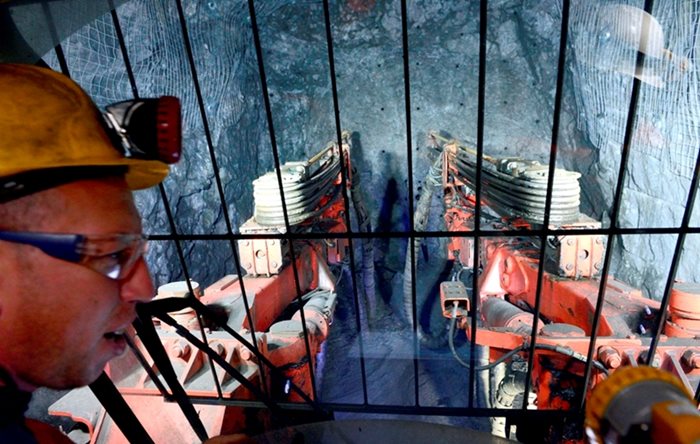
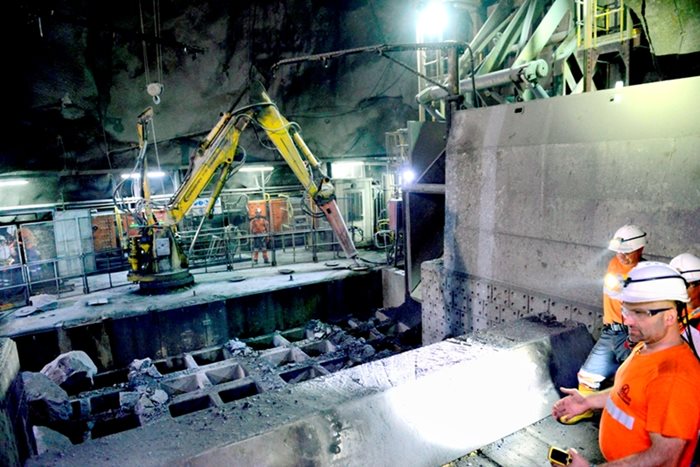
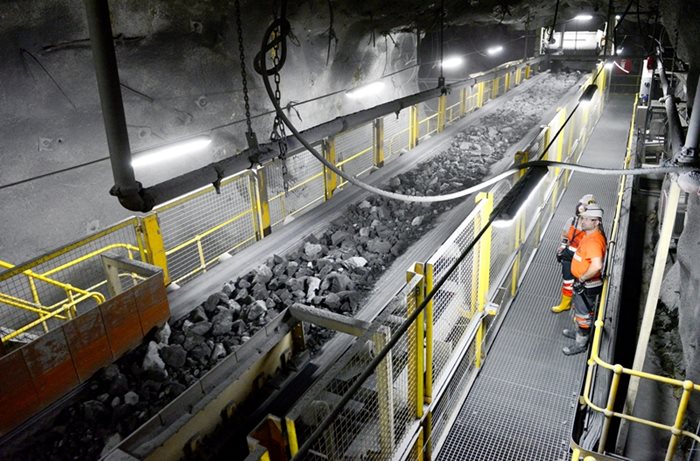